Innovative Injection Mold Tools: The Backbone of Modern Manufacturing
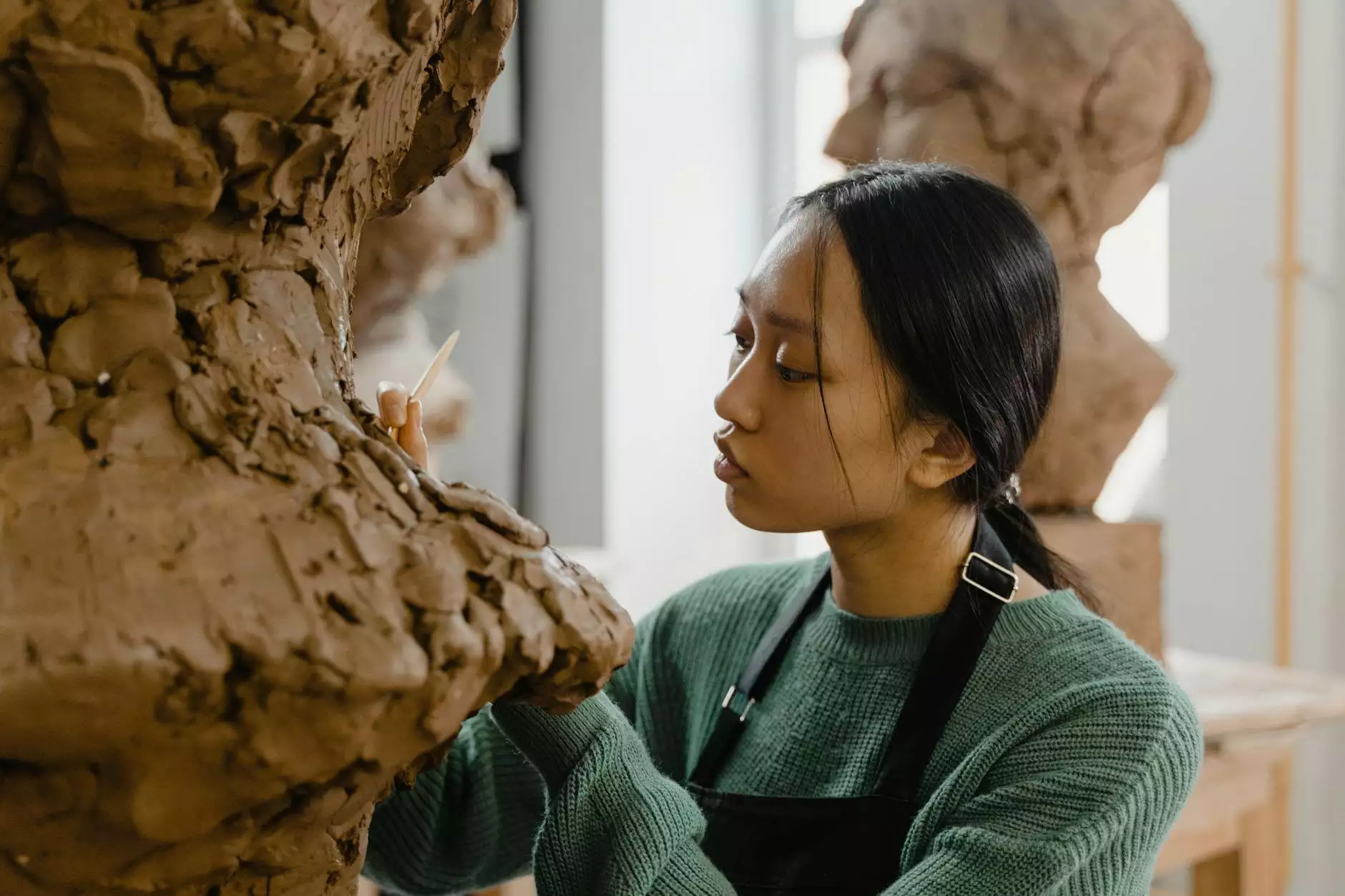
Understanding Injection Mold Tools
Injection mold tools are critical components in the manufacturing industry, particularly for businesses in the metal fabricators category. These tools enable manufacturers to create high-precision parts for a variety of applications, including automotive, consumer goods, and industrial equipment. The process involves injecting molten material into a mold, allowing for intricate designs and efficient mass production.
The Importance of Injection Mold Tools
The functionality of a manufacturing operation can be significantly enhanced by investing in high-quality injection mold tools. Here are some compelling reasons why these tools are essential:
- Precision Manufacturing: Injection mold tools provide unparalleled accuracy, ensuring that each component produced meets exact specifications.
- Scalability: With the right tools, businesses can easily scale production from prototypes to full-scale manufacturing without compromising quality.
- Cost-Efficiency: Once the mold design is finalized, the cost per unit decreases significantly, making it a cost-effective option for mass production.
The Process of Injection Molding
The process of injection molding consists of several key steps:
- Design: The process begins with the design of the mold, which requires collaboration between engineers and designers.
- Injection: Molten material, usually plastic or metal, is injected into the mold cavity.
- Cooling: The material is allowed to cool and solidify, taking the shape of the mold.
- Ejection: Once cooled, the mold opens, and the prepared part is ejected.
- Finishing: Additional processes may be needed, such as trimming and surface finishing.
Materials Used in Injection Molding
Various materials can be used for manufacturing injection mold tools. Each material offers unique properties that can influence the final product's quality and performance. The common materials include:
- Steel: Known for its strength and durability, steel molds can withstand high temperatures and pressures.
- Aluminum: Lightweight and easy to machine, aluminum molds are perfect for lower-volume productions due to faster turnaround times.
- Composites: These materials offer enhanced strength while being lighter than metals, a growing choice in high-performance applications.
Key Benefits of Using Injection Mold Tools
Invest in injection mold tools offers numerous advantages for businesses, particularly for metal fabricators seeking to improve their operational efficiency. Here are some of the most significant benefits:
- High Efficiency: Once set up, injection molding is a fast process that can produce thousands of parts per hour.
- Design Flexibility: Complex geometries and intricate designs can be achieved, which would be impossible with traditional manufacturing methods.
- Material Variety: A wide range of materials can be used, allowing manufacturers to choose the best-suited material for their product needs.
- Reduced Waste: The process is highly efficient, often leading to less waste than other manufacturing methods.
Trends in Injection Mold Tool Technology
The field of injection mold tools is continually evolving, with new technologies enhancing production processes. Some of the emerging trends include:
1. 3D Printing of Molds
3D printing technology is revolutionizing how molds are created, allowing for rapid prototyping and reduced lead times. This technology is particularly beneficial for short-run productions and complex designs.
2. Smart Manufacturing Integration
The advent of IoT (Internet of Things) has paved the way for smart manufacturing. By integrating sensors and software into the molding process, manufacturers can monitor performance in real-time, enhancing maintenance and reducing downtime.
3. Sustainable Practices
There is a growing emphasis on sustainability within the manufacturing industry. Eco-friendly materials and recycling programs are becoming more commonplace, encouraging businesses to adopt environmentally friendly practices.
Choosing the Right Injection Mold Tool Supplier
Selecting a reliable supplier for injection mold tools is vital for long-term success. Here are key factors to consider when making this important decision:
- Experience: Look for suppliers with a proven track record in the industry and a deep understanding of your specific needs.
- Customer Support: Exceptional customer service and support ensure that any issues that may arise can be addressed quickly and effectively.
- Quality Assurance: A commitment to quality assurance means you can trust that the molds will be manufactured to the highest standards.
- Custom Solutions: The ability to provide custom solutions tailored to your unique specifications can give you a competitive edge.
Investing in Injection Mold Tools: A Smart Business Move
For metal fabricators and manufacturers alike, investing in high-quality injection mold tools is not just a choice, but a strategic business move. The benefits of improved efficiency, cost reduction, and enhanced design capabilities lead to a superior competitive advantage in the marketplace. With continuous advancements in technology and increasing demands for high-quality products, the importance of these tools cannot be overstated.
Conclusion
In conclusion, injection mold tools represent a crucial aspect of modern manufacturing, particularly within the realm of metal fabricators. By employing these tools, businesses can significantly enhance their production capabilities, maintain competitive pricing, and meet evolving customer demands. Embracing innovation in this area will undoubtedly yield positive returns and foster sustainable growth in the manufacturing sector.